Druckfedern sind Maschinenelemente, die sich unter Belastung gezielt verformen und bei Entlastung wieder die ursprüngliche Gestalt annehmen. Die technische Feder findet Anwendung in Fahrzeugen, feinmechanischen oder elektrotechnischen Apparaten, in Kraftmaschinen, Werkzeugmaschinen oder landwirtschaftlichen Maschinen, in medizinischen Geräten oder Haushaltsgeräten. Oft beeinflusst das störungsfreie Arbeiten der Federn die Funktion des gesamten Gerätes oder Maschinenteils.
Bei den technischen Federn gibt es eine Vielzahl von Ausführungsformen
und
Schraubenfedern werden in 3 Hauptgruppen unterteilt:
- Druckfedern
- Zugfedern
- Schenkelfedern
Je nach Fertigungsverfahren unterscheidet man zwischen kalt- und warmgeformten
Federn. Bis
Kaltgeformte Federn werden meist aus patentiert-gezogenem unlegierten Federdraht
nach
Um die Dauerfestigkeitseigenschaften wesentlich zu verbessern, werden fertige Federn kugelgestrahlt. Dadurch wird deren Lebensdauer stärker erhöht, als durch Wahl einer besseren Drahtsorte. Im Allgemeinen werden Federn geölt oder gefettet vom Hersteller ausgeliefert.
Druckfedern werden in der Regel rechtssteigend ausgeführt. Um die Federkraft auf die Anschlussteile optimal übertragen zu können, wird bei kaltgeformten Schraubendruckfedern die Steigung an der jeweils auslaufenden Windung vermindert.
Um ein möglichst axiales Einfedern bei unterschiedlichen Federstellungen zu erreichen, werden an den Stirnflächen die Drahtenden plan geschliffen.
Kaltgeformte Druckfedern bestehen aus n ≥ 2 wirksamen federnden Windungen mit in der Regel konstanter Steigung und zusätzlich aus 2 nicht federnden Windungen.
Da für die Berechnung die Art der Beanspruchung maßgebend ist, werden die Federarten nach ihrer vorwiegenden Beanspruchung unterschieden. Bei Druck- und Zugfedern verursacht die Krafteinleitung im Werkstoffquerschnitt hauptsächlich eine Torsionsbeanspruchung.
Drehfedern und Tellerfedern erfahren durch das Einleiten einer äußeren Kraft im Federquerschnitt überwiegend eine Biegebeanspruchung. Andere auftretende Beanspruchungen können meist vernachlässigt werden.
Die Eigenschaften der Federn werden nach ihrer Kennlinie unterschieden.
Hierbei geht es um die Abhängigkeit der Feder
Unter der Federrate R versteht man die Steigung der Federkennlinie im Federdiagramm. Bei linearer Kennlinie ist die Federrate konstant. Federn mit gekrümmter Kennlinie weisen eine veränderliche Federrate auf.
Viele Federn sind aufgrund ihrer Flexibilität in mehreren Richtungen verformbar. Aus diesem Grund wird je nach Kraftrichtung (Freiheitsgrad) des freien Federendes zwischen Längs-, Quer- und Drehfederrate unterschieden.
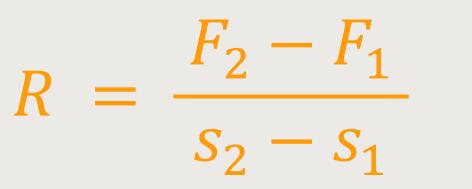
Beim Spannen einer Feder wird Arbeit verrichtet, welche die Feder beim Entspannen wieder abgibt. Die Federarbeit ergibt sich stets als Fläche unterhalb der Federkennlinie. Bei einer linearen Kennlinie gilt für Druck- und Zugfedern:

Wie bei allen mechanischen Bauteilen wird auch das Federungsverhalten durch Reibung beeinflusst. Diese Reibungskräfte wirken einer Rückverformung entgegen. Bei einer Wechselbeanspruchung äußert sich dies in Form einer sogenannten Hystereseschleife. Hierbei verlaufen die Kennlinien während der Druckbelastung und der Druckentlastung versetzt zueinander, ähnlich wie bei der Kontur einer Bohnenschote.
Darüber hinaus wird ein Teil der Federarbeit in Wärme umgewandelt und geht damit verloren. Da dies insbesondere bei Messverfahren vermieden werden soll, ist bereits bei der Konstruktion einer Baugruppe auf die Anordnung und Gestalt der Federn zu achten.
Vor einer „Relaxation” spricht man, wenn zum Beispiel eine Druckfeder bei höherer Temperatur zwischen parallelen Platten um einen bestimmten Betrag zusammengedrückt wird und die Federkraft mit der Zeit allmählich abnimmt. Dieser Kraftverlust nimmt mit steigender Temperatur und Spannung zu. Aufgrund der Relaxation des Werkstoffes kommt es zu einer plastischen Verformung, die sich bei konstanter Einbaulänge als Kraftverlust darstellt.
Der Kraftverlust wird bezogen auf die Ausgangs
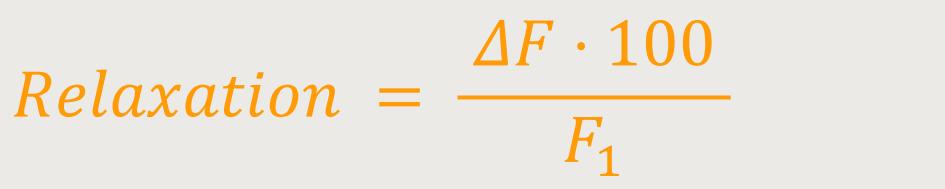
Wenn hohe Anforderungen an die Konstanz der Federkraft gestellt werden, muss ein möglicher Kraftverlust vom Konstrukteur mit einbezogen werden.
Bei einem Federentwurf verfolgt man das Ziel, unter Berücksichtigung aller Umstände, die für die Aufgabenstellung wirtschaftlichste Feder zu finden. Dies wird unter anderem beeinflusst durch den zur Verfügung stehenden Raum und die geforderte Lebensdauer. Hierbei gilt es, folgende Anforderungen zu berücksichtigen:
- Belastungsart (statisch oder dynamisch)
- Notwendige Kräfte und Federwege
- Vorhandener Einbauraum
- Toleranzen
- Einbausituation (Knickung, Querfederung)
- Lebensdauer
- Einsatztemperatur
- Umgebungsmedium
Eine technische Feder wird in zwei Schritten ausgelegt:
Schritt 1: Funktionsnachweis
Zunächst werden Parameter für Federrate, Kräfte, Federwege und
Schwingungsverhalten festgelegt.
Schritt 2: Festigkeitsnachweis
Anschließend werden die zulässigen Spannungen ermittelt und es erfolgt
ein Dauerfestigkeitsnachweis.
Die Schritte erfolgen in sich wiederholdenden Rechenvorgängen. Besonders geht um die Fragestellung, ob die Feder statisch, schwellend oder dynamisch beansprucht wird. In den meisten Fällen wird die Feder vorgespannt sein. Bei dynamisch beanspruchten Federn kann es zu einer periodischen Schwellbelastung kommen oder zu schlagartigen Kraftänderungen.
Bei der Dimensionierung einer Feder müssen die Grenzwerte der Beanspruchung festgelegt werden. Hierfür werden die Festigkeitswerte der Werkstoffe herangezogen. Gerade bei einer technischen Feder ist es sinnvoll, einen Sicherheitsfaktor mit einzubeziehen. Daraus ergibt sich die zulässige Grenzspannung.
Wird beispielsweise bei vorhandener Schubspannung der zulässige Wert überschritten, tritt eine bleibende Verformung der Feder ein. Dadurch verringert sich die ungespannte Länge, was in der Federntechnik als „Setzen” bezeichnet wird. Diese Gefahr wurde bereits im vorherigen Kapitel unter dem Stichwort Relaxation angesprochen. Um diesem Effekt entgegenzuwirken, werden die Druckfedern um den zu erwartenden Setzbetrag länger gewunden und später auf Blocklänge zusammengedrückt. Durch dieses sogenannte „Vorsetzen” wird eine bessere Werkstoffauslastung und höhere Belastung ermöglicht.
Für die Auslegung statisch oder schwellend beanspruchter Federn wird die
Schub
Korrigierte Spannung:
Anschließend müssen die zulässigen Spannungen miteinander verglichen werden.
Die Werte für die Mindestzugfestigkeit Rm sind von der Drahtstärke abhängig und in den Normen der entsprechenden Werkstoffe zu finden.
Da sich Druckfedern bis zur Blocklänge zusammendrücken lassen
müssen, ist die zulässige Spannung bei Blocklänge
τczul zu ermitteln. Bei dynamischer Beanspruchung
müssen zusätzlich Unter- und Oberspannung
Alle dynamisch beanspruchten Federn mit einer Drahtstärke
Die Blocklänge kann nicht unterschritten werden, weil die Windungen bereits fest aneinander liegen. Andernfalls kommt es zu einem Versatz der Windungen, wodurch ein linearer Kraftverlauf sowie eine dynamische Belastbarkeit nicht mehr gewährleistet sind.
⇦ Kapitel Kapitel ⇨